I interviewed Gordon Downes, the founder and CEO of NYSHEX, an innovative company providing technology solutions to address major challenges in the ocean container shipping industry. With 80% of the top 10 ocean container carriers and many shippers already using the NYSHEX platform, it has significant implications for reducing expected lead times, lead time variance, safety stock, and out-of-stocks for shippers, while also enabling carriers to utilize their equipment more efficiently.
What impressed me about Gordon is how his 12 years of experience at Maersk, the world's largest ocean container carrier, combined with his time at SABMiller/AB InBev, the world's largest beer shipper, gave him unique insight into the problems facing both carriers and shippers. From the carrier side, he saw how no-show bookings and overbooking led to vessels sailing underutilized. From the shipper perspective, he witnessed the costly consequences of containers arriving late.
Eight years ago, recognizing that other industries had solved similar problems using technology, Gordon founded NYSHEX to collect, cleanse and harmonize data from various supply chain partners to provide a shared system of record. This enables carriers, shippers, NVOCCs and 3PLs to all have the same set of facts to identify the root causes of problems, rather than relying on incomplete information and engaging in blame games that strain relationships.
Some of the key problems NYSHEX addresses include determining what went wrong when a container doesn't show up as planned - was the container not loaded, picked up late, or documentation not produced on time? The platform captures data on all the steps prior to container movement, not just basic visibility, to provide a complete picture. It then generates alerts and workflows to flag at-risk containers while there is still time to take corrective action.
By improving planning, execution and communication across the supply chain, NYSHEX reduces waste that negatively impacts both carriers and shippers, such as vessels sailing light and shippers facing production delays. Carriers benefit from better vessel utilization, reduced workload dealing with exceptions, and strengthened customer relationships. Shippers gain the ability to provide carriers with more reliable volume forecasts to secure space and equipment allocations.
I see huge potential for shippers to leverage the rich data and analytics from NYSHEX to optimize inventory, similar to what happened in the quality management era when businesses redesigned processes to eliminate sources of defects. With granular data on transit time distributions and delay patterns that were never available before, shippers can reduce safety stock while improving service levels. This can free up significant amounts of capital, especially important in the current high interest rate environment.
While change is hard in an industry that operates on processes largely unchanged for decades, Gordon emphasized how the value NYSHEX delivers is a true win-win. By focusing first on tactical, tangible problems to demonstrate results, then expanding to more strategic issues over time, the company has steadily grown to processing 2% of global container volume, with ample room for further growth.
I'm excited by the potential of neutral, third-party platforms like NYSHEX to foster trust, transparency and collaboration that lifts performance for all supply chain participants. With the industry's structural challenges not going away, I believe we will see accelerating adoption of such solutions to enable the responsive, resilient and efficient supply chains required for success in today's turbulent business environment.
Transforming Ocean Shipping: How NYSHEX's Innovative Platform Drives Supply Chain Efficiency
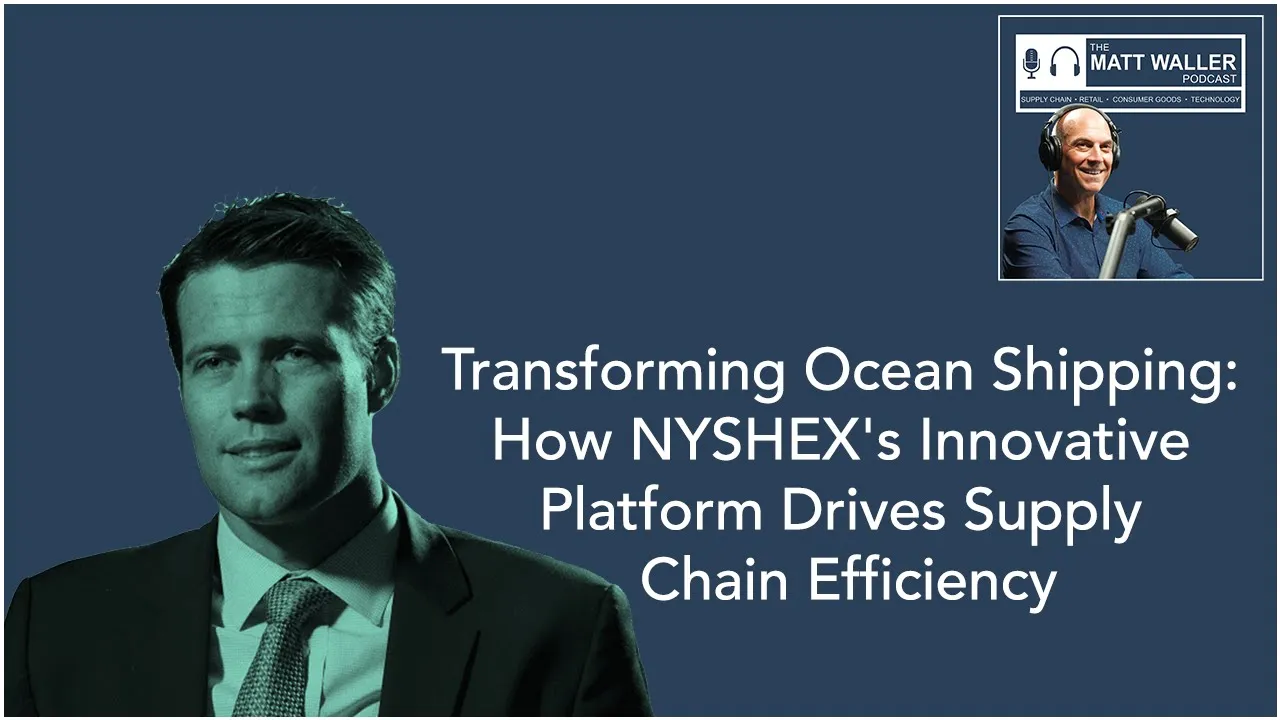
Member discussion: